What is Orbital Welding?
Orbital welding is the automatic welding of tubes or pipe in-place with a rotating tungsten electrode. Orbital welding equipment using the Gas Tungsten Arc Welding (GTAW) process can be used for simple fusion welding, and with the addition of filler wire.
Orbital tube welding was developed in the 1950s, replacing compression fittings and manual welds in the aerospace industry. Technological advancements have made programming and operation simple. Enclosed weld heads can operate on diameters 0.125” (3mm) up to 6 “ (168.3mm), and open weld heads using interchangeable guide rings can mount on a pipe of any diameter.
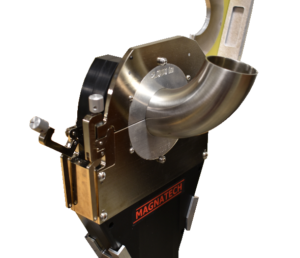
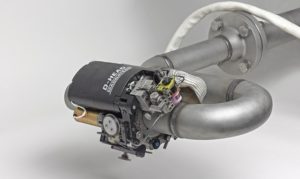
The lack of skilled workers and increasingly stringent welding codes have left mechanical contractors, fabricators and manufacturers searching for the solutions that orbital welding provides.
Orbital Welding Benefits
Consistency and Repeatability
Unlike manual welding, the orbital welding process produces welds that meet industry code acceptance criteria. Consistent bead size and full penetration create smooth surfaces that prevent microbiological growth and possible contamination of the product, a requirement of ASME BPE. Multipass welds with the addition of added filler wire will meet the rigorous pressure and process pipe codes of B31.1 and B31.3.
Cleanliness
An orbital fusion weld head creates a sterile, enclosed environment for a tube weld. With proper purging techniques, the discoloration associated with oxidation of stainless and high-nickel alloy is easily prevented.
Versatility
Orbital welders are ideal for applications where the tube or pipe cannot be rotated, have poor arc visibility, or are located in a hard to reach place. The automated welding process will improve operator comfort and safety, eliminating repetitive motion injuries.
Productivity
Many industry studies have found that a manual welder averages a 30% “arc on” time. Orbital welding equipment can average a 75-80% efficiency; as it eliminates the fatigue factor.
Documentation
The orbital welding power supply can manage and print weld schedules to keep accurate and complete documentation of welds.
Practical Applications for Orbital Welding
- Tube to Tube
- Tube to Fitting
- Fitting to Fitting
- Pipe to Pipe
- Pipe to Fitting
- Nickel alloys, Copper Nickel, Monel, Duplex Stainless
- Weld Buildup Repairs
If you don’t see your specific application, please call (860) 653-2573 to talk to an orbital welding specialist to investigate solutions.